Upgrading from a peg board to this french cleat wall is a game changer. There’s so much flexibility, components can be made with scrap wood instead of having to buy metal hangers. They’re also a lot stronger and looks good too.
What is a french cleat?
If you’re a beginner like me and you don’t know what a french cleat is, lemme google that for you. A french cleat is basically a piece of wood or anything that is mounted on the wall that can hold another piece. Usually the part that goes on the wall has a 45 degree angle that another piece can be mounted on. That other piece has an opposite angle and is attached to whatever you’re mounting on the wall.
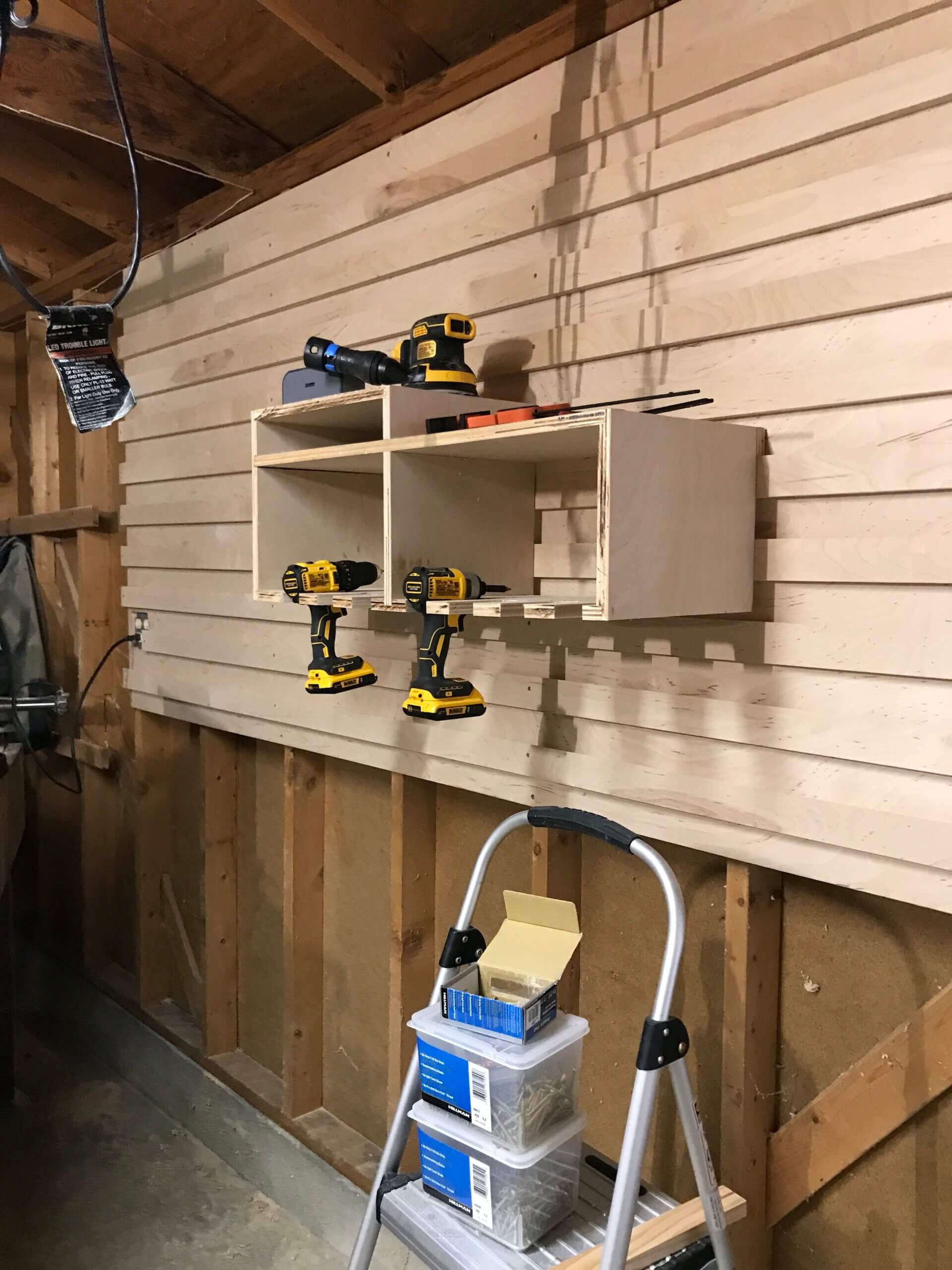
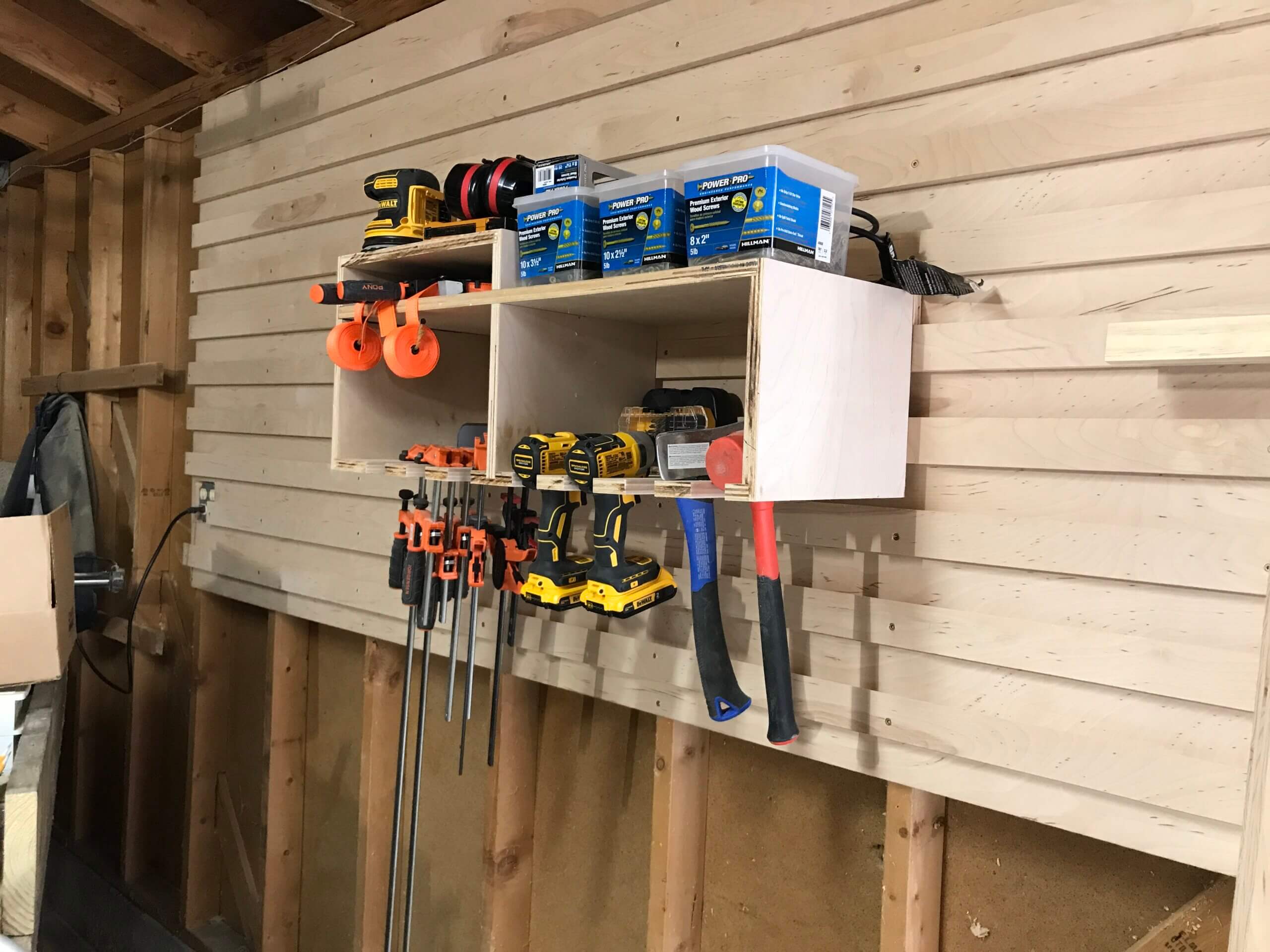
Customization
The first obvious advantage is being able to build a container or a holder that suits your specific needs. Whether you need space for your circular saw, clamps, various boxes of screws, you can have it. The only limitation here is your imagination. These things can even vary in weights, just look at how much stuff I was able to put on my first multi-tool organizer.
Ease of use
I love that I can now move anything around as I please. If I need to move things based on my current project, I can do that. Likewise, should I find the need to move anything out of the way, I can easily do that too. For example, I built a holder for my squares, if I am away from the wall and I’m finding that I need to keep referencing a square, I can choose to remove the holder and bring that closer to my work area instead of constantly losing them.
Final thoughts
Overall, I’m surprised at how easy this is to build using only one and a half sheets of plywood. I should’ve done this as my first project. If you are just starting out, I would suggest tackling this one early to get a jump on organization before your space gets out of hand like mine did.
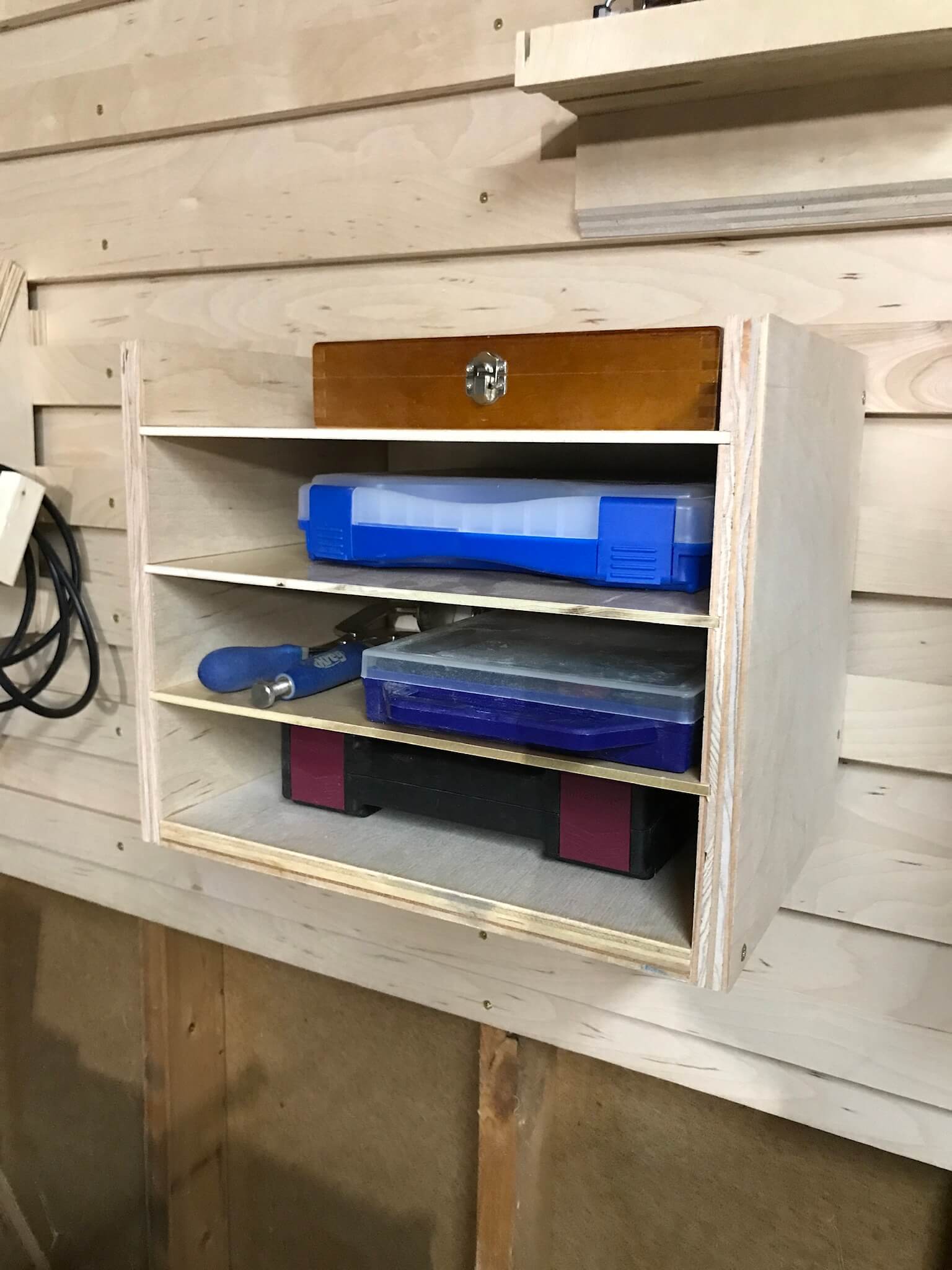
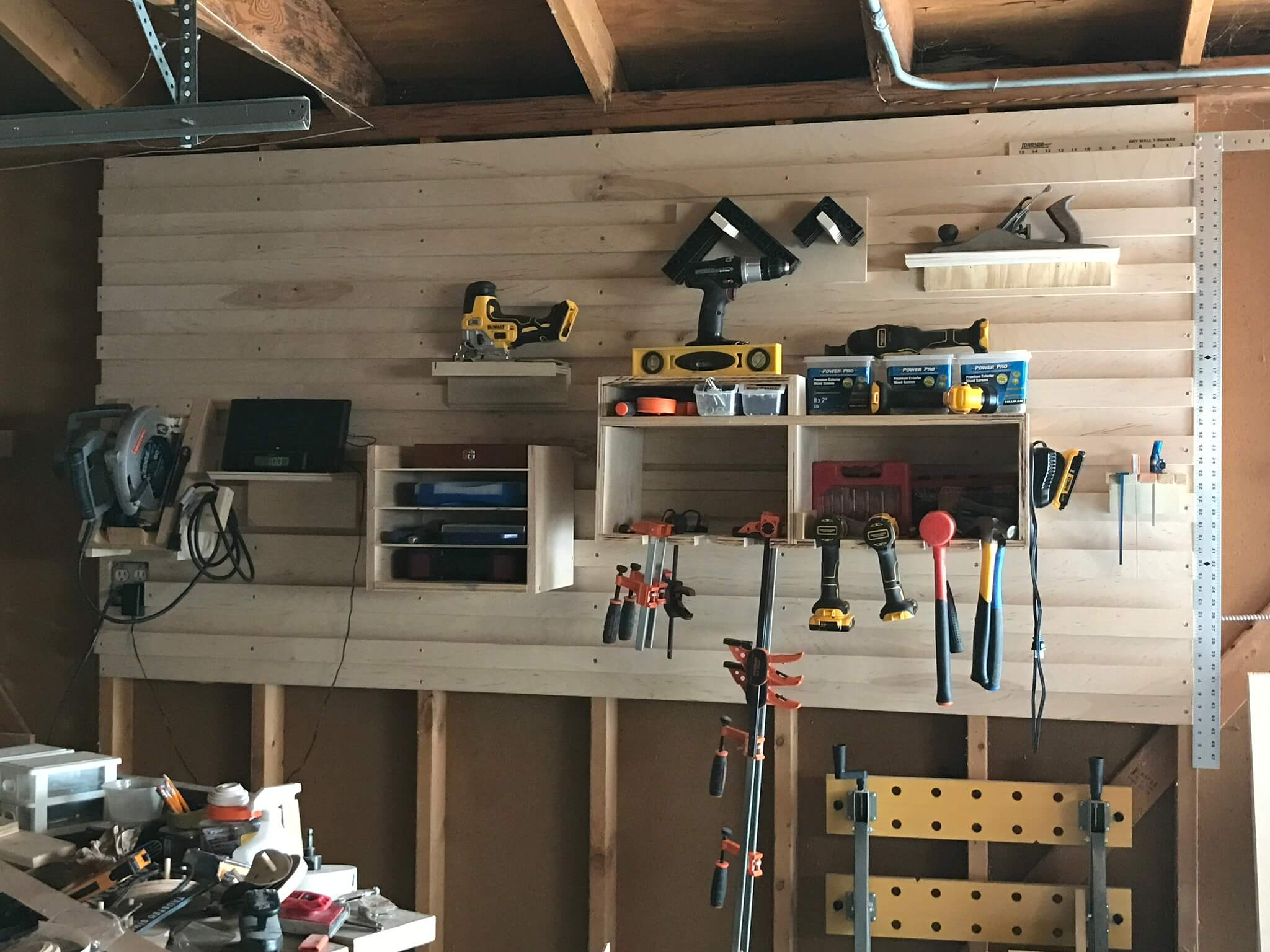
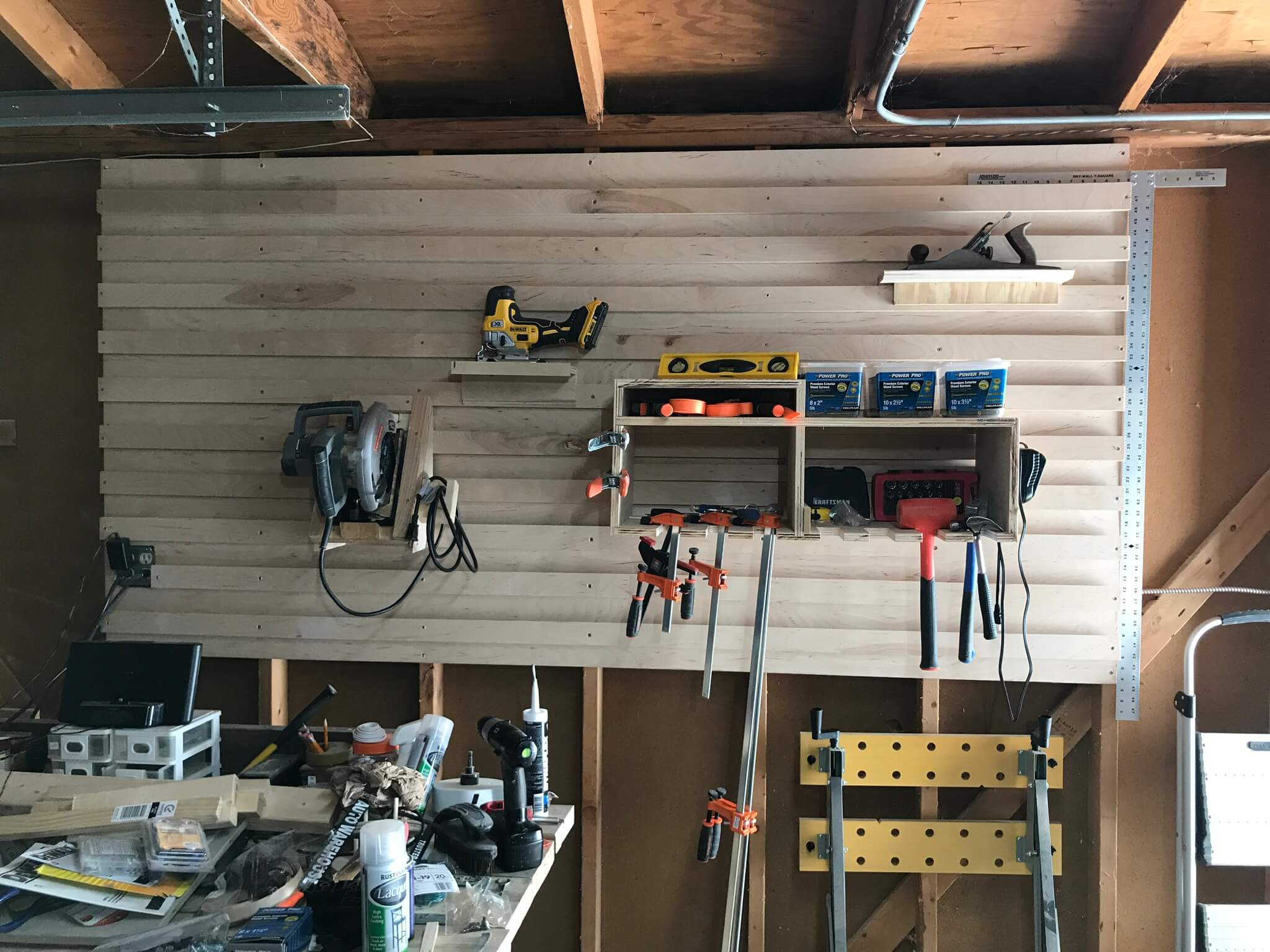
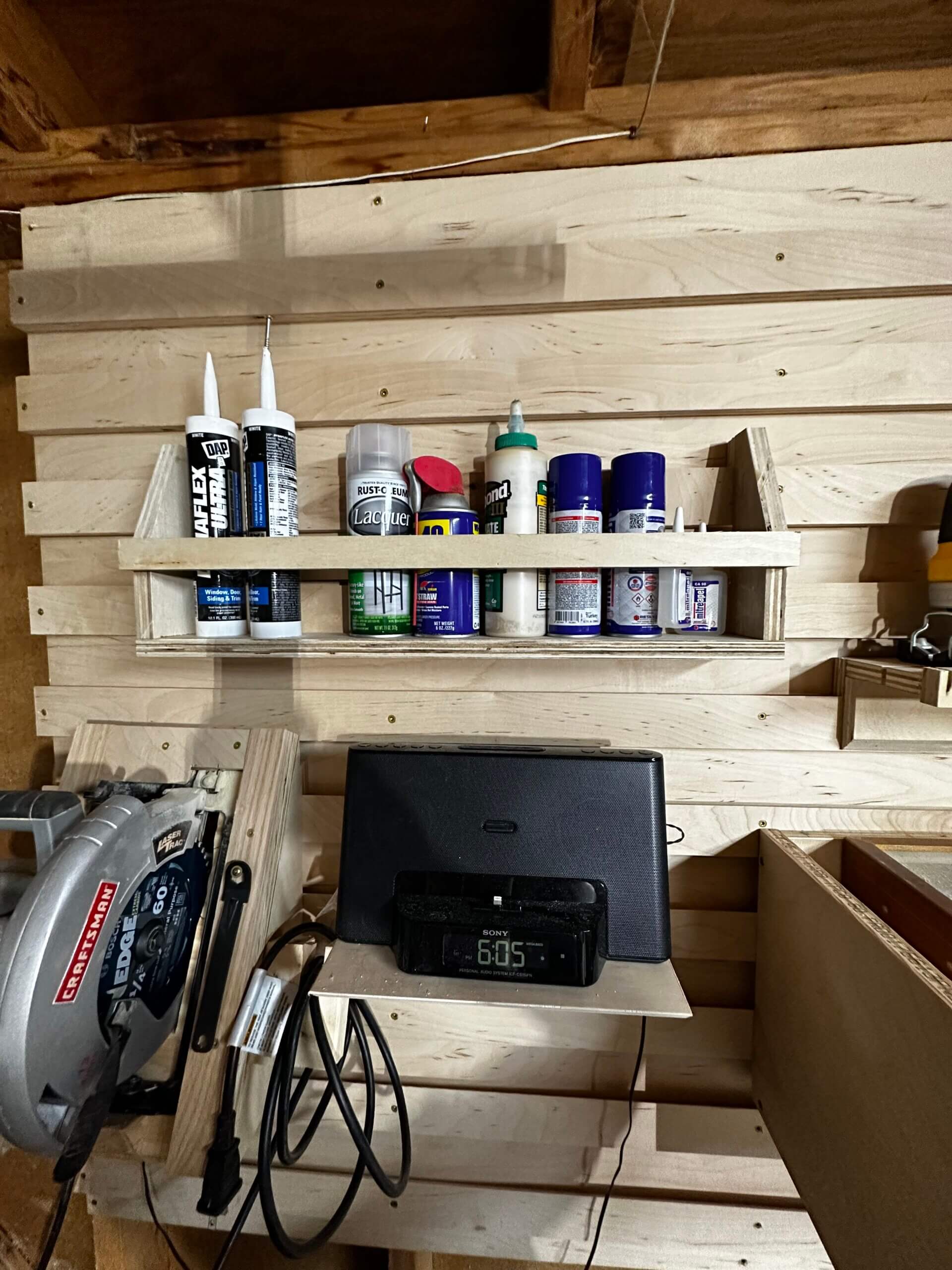
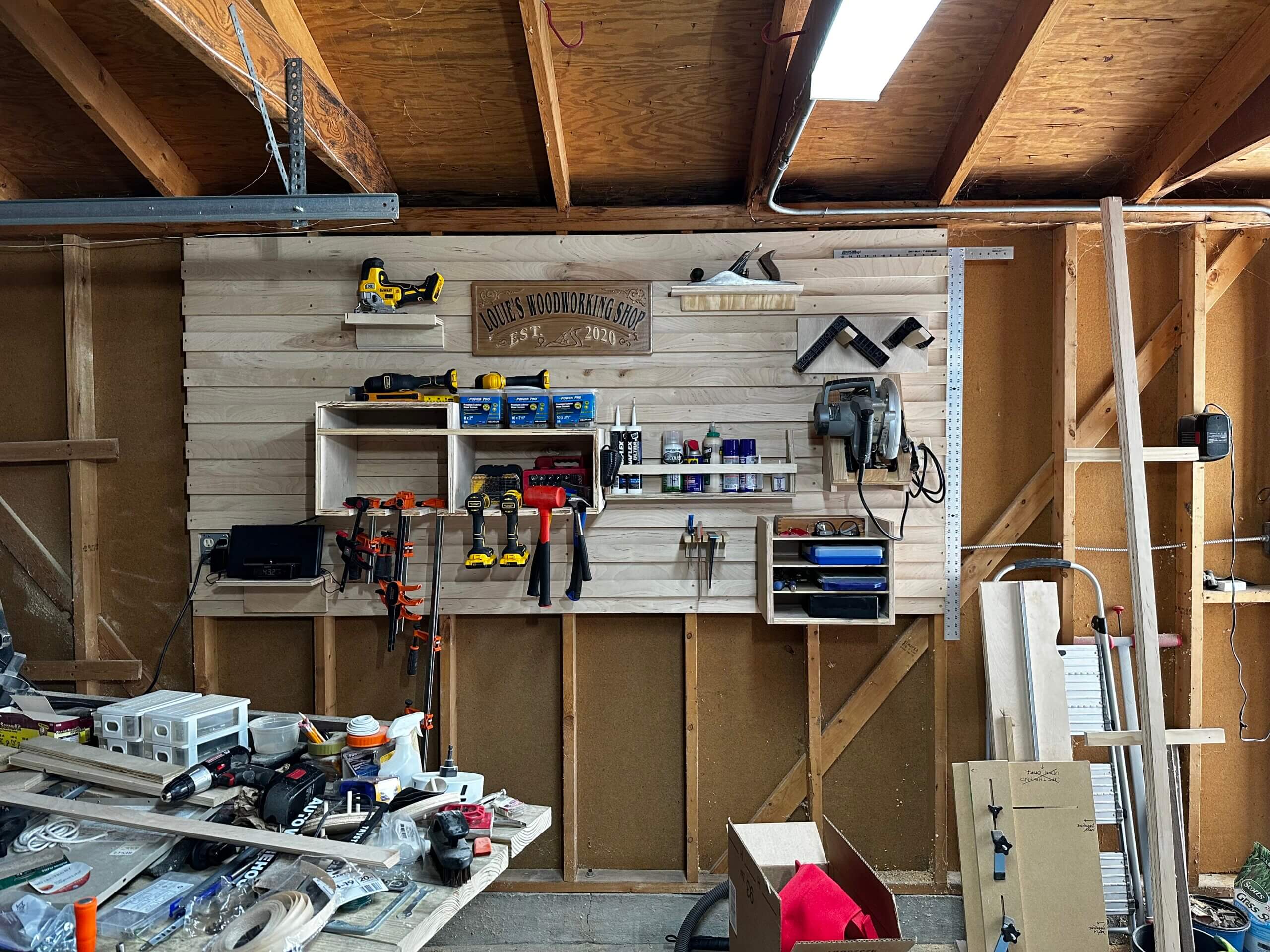